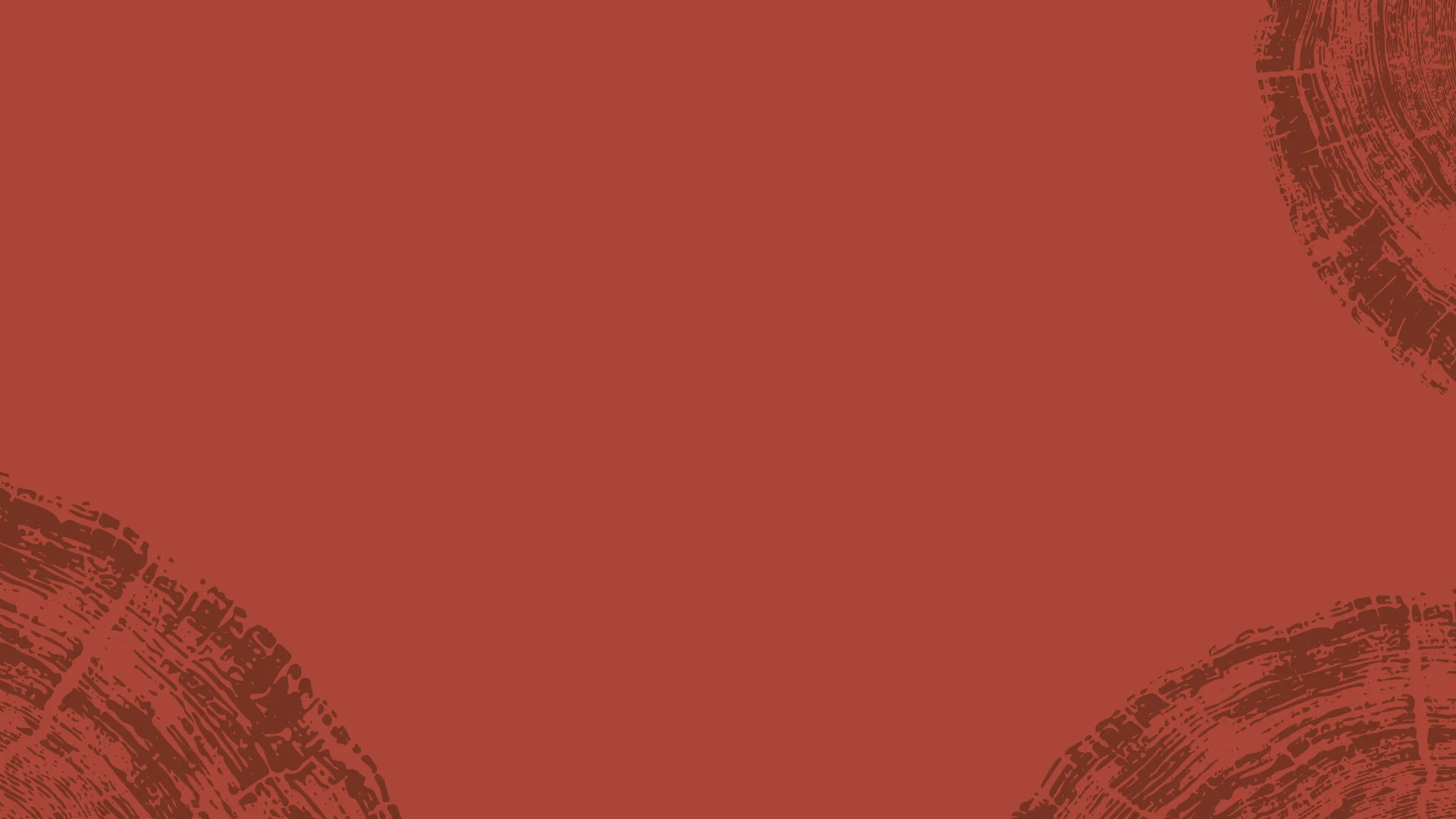
Products made honestly, thoughtfully, and with pride in every step of the process.
Sourcing Material
I often collect turning material from fallen trees. Trees that have died during the harsh Colorado winter, Aspens and Cedars knocked down by falling pines or high winds, fast-growing trees cleared from below power lines, and urban trimming and clearing are material sources for my work.
I also look for quality discarded solid wood consumer goods that are being discarded. Often, this material is in excellent condition and can be segmented to create pieces that are very unique and special.
Preparing the Log
Before work can start on a blank piece of timber, I make sure the wood is properly dried and prepped for turning to ensure that a quality and long-lasting product is made. I cut the tree into manageable sizes and treat the end grain with Anchor Seal to ensure a slow and consistent drying time. Drying the wood is an art all to itself, and the process can take as long as a year or two depending on the hardness of the species.
Planning and Preparation
Over time I have learned to allow the design of my finished pieces to take shape as the turning process unfolds. I will take note of the unique qualities of the wood I am about to shape, and then I will allow the material to dictate where the design goes. This process allows for the unique, natural qualities of every piece of wood to be highlighted, and means that every piece from my studio is one of a kind.
Turning
The turning process for me is a thoughtful conversation between myself and the material. I observe the unique characteristics of the wood as the layers of material are cut away, and I work to highlight those details and story through the design of the piece.
I first learned turning utilizing carbon tipped tools and have more recently begun using more traditional chisels for my pieces.
Finishing
I love the look and feel of a natural wood finish. The majority of my products have a simple application of food grade mineral oil or butcher block oil to bring out the rich colors of the grains and protect the wood.
I will sometimes use finishing techniques such as an epoxy or mineral filler to seal cracks or holes prior to sanding and polishing. These methods help to preserve the natural inconsistencies found in the wood.
The most important and final step is sanding. I use a polishing technique that takes the piece from a 400 grit sanded finish to a natural gloss finish through a three step polishing wheel process.
I have been told that I spend too much time finishing and should produce my items quicker, but I cannot bring myself to do that.
I expect every product I sell to be of exceptional quality and work hard to make sure the finished product meets that standard.